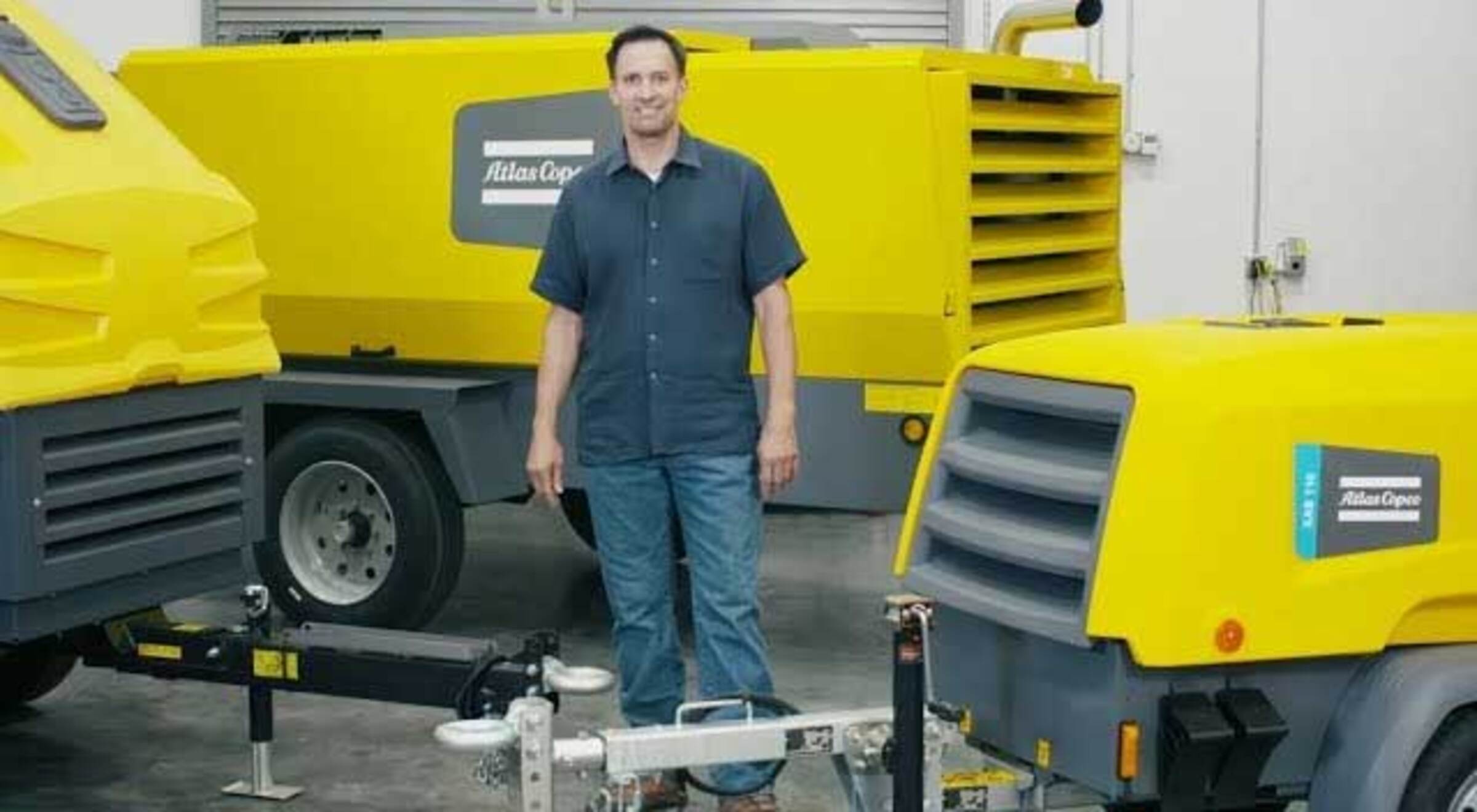
Understanding the Range and Operation Principles
When it comes to compressed air systems, Atlas Copco stands out as one of the global leaders in quality and innovation. Choosing a reliable compressor depends on several key factors, including the intended application, required air pressure, and energy efficiency. Atlas Copco offers a wide variety of compressor types—rotary screw, piston, and centrifugal models—all engineered to meet specific industrial demands. The working principle typically involves drawing in air, compressing it mechanically, and storing it in a tank or delivering it through a pipeline for direct use.
Different compressors serve different purposes. For example, rotary screw compressors are excellent for continuous-use scenarios such as manufacturing or construction. In contrast, piston compressors are often suitable for short-cycle tasks in smaller workshops. Understanding these operational differences is essential to make a well-informed purchase. For those in search of expert advice and access to trusted Atlas Copco solutions, the platform https://www.ebner-druckluft.de/ provides valuable insights and product offerings tailored to various business needs.
Application Areas and Product Features
- Atlas Copco compressors are found across many sectors, including automotive workshops, food and beverage production, medical facilities, and heavy industry. In the automotive industry, compressors power pneumatic tools and paint systems.
- In healthcare, oil-free models ensure clean air supply, critical for surgical and laboratory environments.
- The food industry requires compressors that guarantee contaminant-free processing. Each application demands a different model with distinct filtration levels, pressure output, and safety standards.
Choosing a compressor also involves comparing features like noise levels, mobility, and maintenance intervals. For operations requiring continuous power, energy-saving technologies such as variable speed drives (VSD) offer tremendous benefits by adjusting motor speed to air demand in real-time. Moreover, compact models with low noise output are preferable for indoor workspaces, while portable units suit on-site job locations.
Comparative Overview of Compressor Types
Compressor Type | Best For | Key Features |
---|---|---|
Rotary Screw | Continuous industrial use | High efficiency, quiet operation |
Piston | Small workshops | Low cost, easy maintenance |
Centrifugal | Large-scale facilities | High flow rates, oil-free options |
Final Considerations
Selecting the right Atlas Copco compressor involves more than just price comparison. You must assess the volume of compressed air needed, the duty cycle of the equipment, and the specific environmental conditions of your operation. Additionally, looking into after-sales support, warranty, and spare part availability can significantly impact the long-term performance and reliability of the compressor system. Atlas Copco remains a trusted name because of its commitment to quality, technological innovation, and customer satisfaction across diverse industries.